Andy Anthony, Managing Director of Monitran, explains how a leading producer of potato crisps is using vibration sensors and an advanced site-wide condition monitoring system to protect machinery, better schedule maintenance and keep production on track.
Crisps production involves a variety of machines with rotating and moving parts, plus flowing water, hot oils and pneumatics. Production runs 24/7 and it is essential to keep all plant and equipment fully functional as some plants are required to process several tonnes of potatoes per day. The servicing and repair of equipment needs to be carefully scheduled, and unexpected failures avoided, which is why many crisps producers employ condition-based predictive maintenance strategies that look for changes in vibration levels to detect component wear and developing faults in machinery.
In August 2013, one of the UK’s leading producers of crisps awarded a contract to Drive Management Services (DMS) to design and install a hard-wired site-wide conditioning monitoring (CM) system.
Collaborating under a Diagnostic System Integrator (DSI) partnership, formed in 2012, sensors OEM Monitran and DMS used their combined expertise to identify how many sensors, and which types, should be used to protect each asset.
They determined that a total of 161 accelerometers would be required. Of these, 136 are Monitran MTN/2200 general purpose, top-entry accelerometers with AC outputs. Sealed to IP67, these sensors have a frequency range of 0.8Hz to 12kHz and an operating temperature range of -55oC to 140oC. In addition, the internal electronics is isolated to minimise noise and afford good bias voltage stability. The remaining 25 sensors are Monitran MTN/1105 high temperature accelerometers, which can be mounted on surfaces at up to 250oC and, in this case, are mounted on a number of hot oil pumps.
Installation of the sensors commenced in November 2013 and was challenging as the work had to be done around the site’s busy production schedules. Also, the wiring (and some 4.5km of screened twin-core was used) had to follow existing cable runs.
Coincidental to the installation of the sensors, Monitran began building five standalone CM units. Working to a detailed asset-sensor-to-channel map, the company programmed and partly pre-calibrated the units in High Wycombe, before taking them to DMS’s premises in Rotherham for a factory acceptance test, for which Monitran was present, by the end user.
Installation of the five CM units commenced in February 2014. All five units connect via Ethernet to two PCs; one in the engineering office and one in the production office. Both PCs run a simple but effective software program, developed by Monitran, which uses a ‘traffic light’ colouring system to reflect each asset’s condition as either ‘Healthy’, ‘Warning’ or ‘Alarm’. The software also allows engineers to view historical data and see how quickly the warning or alarm condition arose; enabling them to make an informed decision on what actions should be taken, and how quickly.
Historical data can also be viewed on the factory floor. Authorised maintenance engineers can open the CM units and access data via a touch-screen display. They can also connect a hand held spectrum analyser to the signal conditioning unit corresponding to the channel of interest to view the raw vibration signature.
The producer’s hard-wired site-wide CM system is currently being commissioned. In addition, the producer has plans to expand its site in the future; in which case the CM system can expand through the addition of appropriate sensors and one or more CM cabinets; which would also be networked to the site’s PCs. The producer is also considering upgrading some of its other UK factories with similar systems.
www.monitran.com
www.dmsinteractive.co.uk
image h
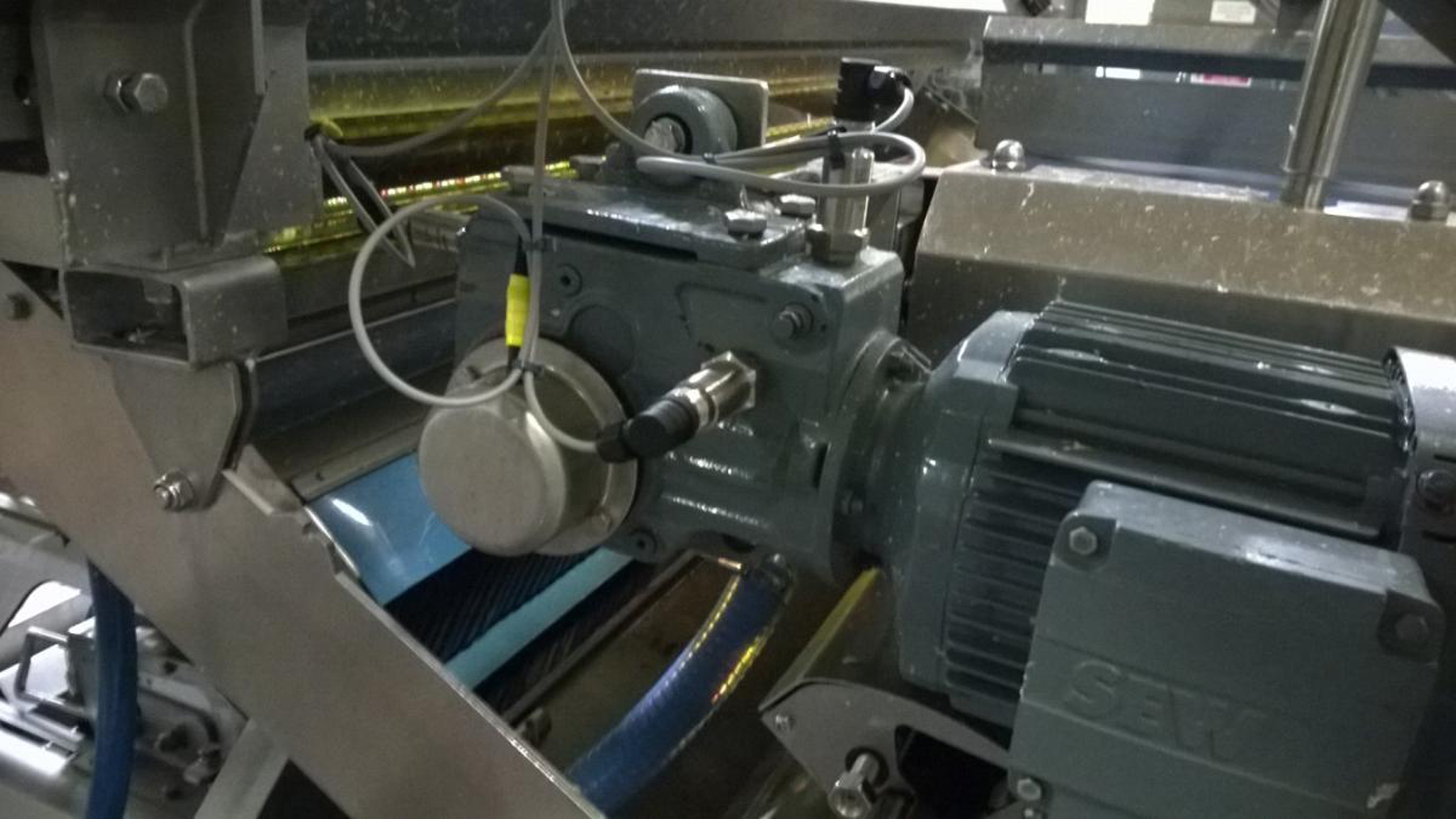
ere
Above, two orthogonally-mounted MTN/2200 general purpose accelerometers with AC outputs monitor gearbox vibration levels.