Condition-based predictive maintenance (CBPM) is becoming increasingly popular within many industries as a practical and cost-effective means of protecting pumps, motors, gearboxes and other machinery. But of all parameters that might be monitored as part of a CBPM strategy vibration is arguably the most useful - advises Andy Anthony, Managing Director of Monitran.
As a strategy, CBPM provides the ideal compromises between failure-based maintenance (a.k.a. “run-to-fail”) and the potentially equally expensive practice of conducting maintenance on a periodic basis irrespective of machine use.
Frequently, a rise, or in some cases a drop, in vibration levels provides the earliest indication that a bearing, gearbox, motor or other electro-mechanical component is in need of maintenance. Moreover, analysis of the vibration signature can reveal the nature of the fault; for example, a broken tooth on a gear or a worn bearing.
Vibration monitoring is of particular use when it comes to protecting plant and machinery that is not only expensive in its own right but is also heavily depended on to keep operations going. One question though is: how often should vibration levels be measured as part of a CBPM strategy?
For instance, a steel mill in the United Kingdom, recognising the usefulness of vibration monitoring, used to conduct surveys on a monthly basis. These surveys included the use of portable measuring instruments to check the vibration levels of, amongst other machinery, fans supplying the furnace’s air/fuel mix and also used to expel waste gases.
During one inspection it was noticed that the vibration levels at the impellor end of one fan were higher than normal. The data was analysed and it was found that the overall RMS vibration amplitude had more than quadrupled in the space of the few weeks since the previous survey.
The fan was displaying symptoms of mechanical looseness; most likely somewhere along the shaft or a shaft-mounted component judging by the vibration signature. Plant staff agreed to take action at the earliest possible opportunity. However, that evening, the fan threw an impellor blade which broke through the fan housing and embedded itself into a nearby control panel.
Had they their time again, those involved in maintenance would not act in any other way. Indeed, based on the information to hand, the best course of action had been taken; as the data captured during the survey would not have condemned the fan and led to an immediate shutdown, impacting on production.
In essence, whilst the vibration signature provided a strong, and as it transpired accurate, indication of what was failing it was not possible to estimate the rate of deterioration. Had vibration levels started rising the day after the previous survey or only a few hours before the one conducted that day? Just where were they on the failure curve?
Had the survey taken place a day later, the impellor blade would of course already have been thrown; and from a seemingly healthy machine going by the previous survey’s readings.
There is therefore much merit in performing condition monitoring all of the time and vibration sensors are increasingly being employed as permanent fixtures to pumps, motors, gearboxes and other assemblies to supply monitoring and control systems with vibration data. Accordingly, alarms can be raised the moment vibration levels warrant investigation and, worst case, machinery can be automatically shut down if vibration levels rise so quickly there is no time to investigate.
There is also another reason for monitoring vibration levels. Vibration is the movement of something, and that requires energy. Hence, if a powered electromechanical assembly is vibrating more than it should be then it will undoubtedly also be less efficient (in terms of power in vs. work achieved) than intended.
For example, Monitran’s vibration sensors were recently used as part of a valve monitoring system for a compressor. Specifically, valve wear can result in a high pressure gas leak into the low pressure side of the system – i.e. it does not physically escape – so the compressor just has to work harder to produce a given volume of compressed gas.
The Pressure is ON
One sector making very good use of vibration monitoring is the water industry, particularly sweater desalination plants using a process called reverse osmosis (RO) to make water for human consumption and agricultural use. While salt can be removed from seawater in a number of ways - including distillation, freezing, dehumidification – RO is used extensively in many countries for producing drinking water.
The RO desalination process requires passing seawater at very high pressure (circa 1,000psi) through a semi-permeable membrane. This requires a great deal of energy and is why most RO desalination plants are located close to power stations.
One country particularly reliant on seawater desalination is Israel. It has three fully operational plants and a further two scheduled to come online shortly. The ones in operation are: Adom, near Ashkelon, which came online in 2005; Via Maris near Palmachim, which came online in 2007; and Omis-Water, near Hadera, which came online in 2009.
Between them the three plants have several hundred high pressure pumps, each of which is fitted with at least one vibration sensor. The majority of these sensors are Monitran MTN/1185 general purpose, top-entry transducers (and figure 1 shows a sensor in situ on a pump in the Adom desalination plant).
These sensors output a direct current (DC), in the range 4-20mA, proportional to velocity. The outputs then feed into PLCs which control the pumps, and in which two pre-determined alarm levels have been set for each sensor. If vibration levels reach the first level an alarm is raised. If vibration levels reach the second and higher level then the PLC automatically shuts down the relevant pump.
Advice
Above, we have cited the use of general purpose sensors with DC outputs. Sensors have a number of characteristics which should be considered during the selection process. In addition to top-entry (as per figure 1), sensors are available where the cable enters from the side. Choosing between top- and side-entry will be governed by how you plan to run the cables. Also, the connection to the sensor can be integral (as per figure 1) or via a connector.
Should you wish to go down the route of monitoring vibration levels at set intervals (i.e. a temporary installation) then sensors are available with magnetic bases. It is essential to use the same sensor in exactly the same position for each reading and you may wish to consider using paired ID tags/labels.
Next, the presence or risk of water, high humidity levels or hazardous atmospheres will steer you towards certain sensor sealing characteristics (IP67, 68...) or intrinsically safe (ATEX, IECEx...) devices. Temperature needs to be considered too, as output drift (with temperature) may be an issue; but only if you intend to operate the sensor close to its declared operating limits. See box ‘Taking Measure’.
In summary
CBPM helps plant/facility owners walk that fine line between “run-to-fail” and over servicing machinery, and there is much to be said for monitoring 24/7.
Also, of all parameters that could be monitored, vibration is perhaps the most useful, as the analysis of vibration signatures can provide an indication of which components are failing or have already failed. With such knowledge you can better schedule maintenance routines and make sure replacement parts/components are delivered in a timely fashion.
There are several different types of vibration sensor available on the market, but selection need not be a daunting process if you follow the above advice regarding characteristics and measure normal operating vibration levels in order to ‘size’ the sensor’s sensitivity; thus enabling you to determine the limits at which to raise an alarm or perform an emergency shutdown.
Monitran
www.monitran.com
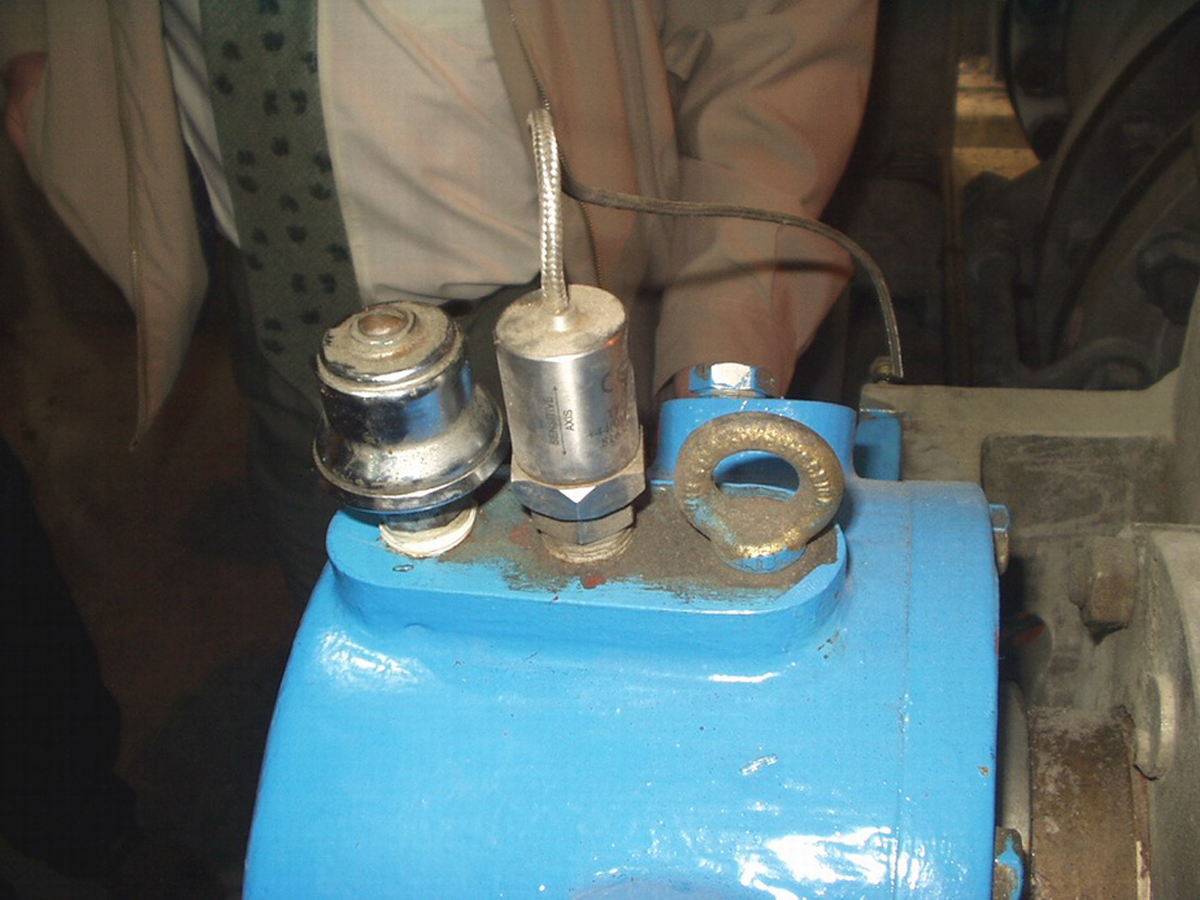
Figure 1. Above, an MTN/1185 vibration sensor in situ on a pump at the Adom desalination plant.
The Vibration Sensor
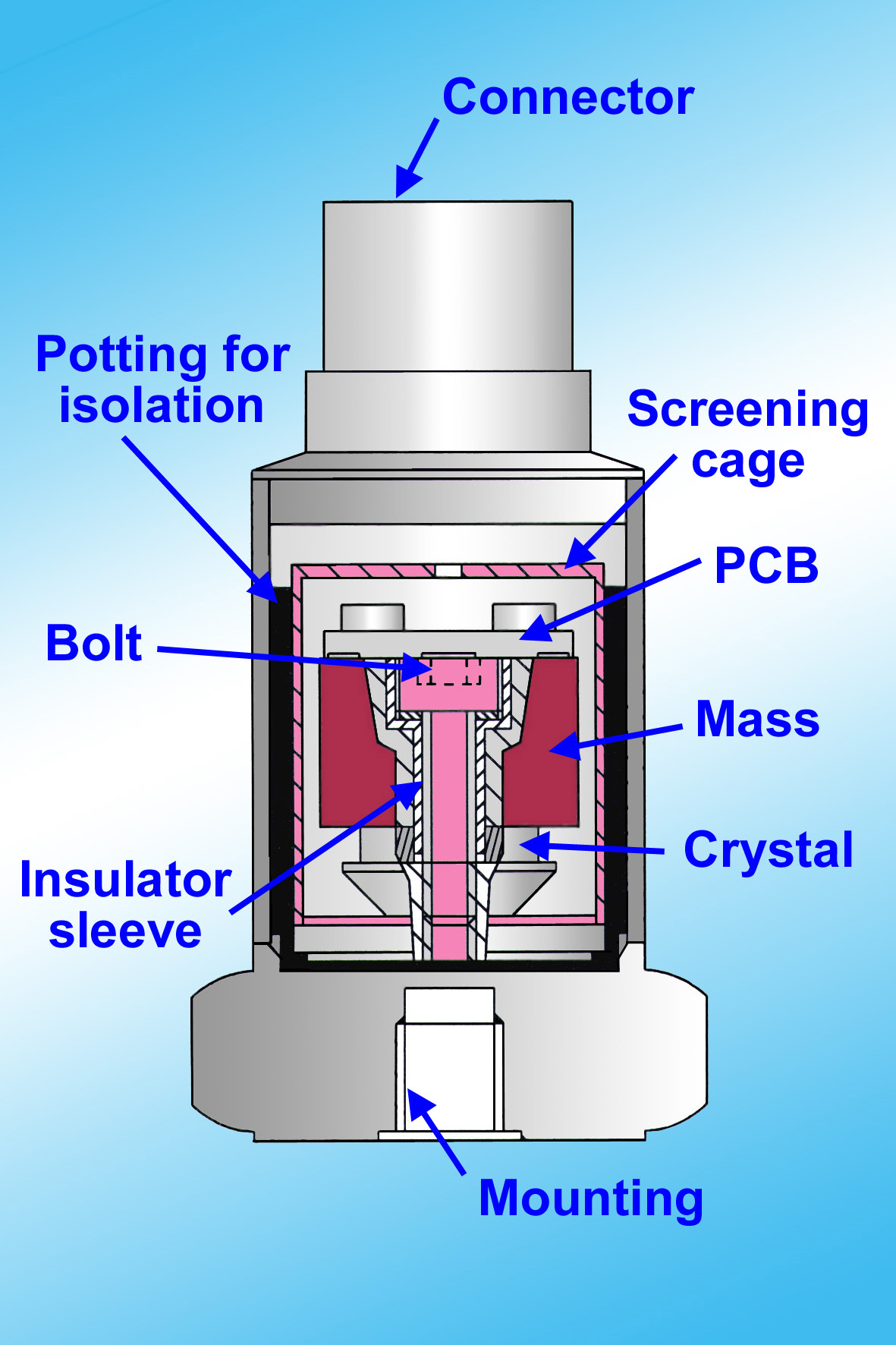
Vibration sensors are typically electronic devices, employing either piezoelectric or piezoresistive technology. Of these two technologies the former is more prevalent in monitoring applications.
In the above cut-away diagram the mass is bonded to a piezoelectric crystal which, when placed under tension or compression, generates an electric charge proportional to the acceleration of the mass; hence why vibration sensors are also referred to as accelerometers.
The electric charge is conditioned by the circuitry (PCB) to produce a more useful output; typically a direct current (DC) in the range 4-20mA for ease or integrating the sensor into a monitoring system or a Programmable Logic Controller (PLC). However, sensors with AC outputs are also popular.
The output (proportional to acceleration in mm/s/s) may also be conditioned to represent velocity (mm/s) or displacement (mm), and sensors are also available with multiple outputs (e.g. acceleration and velocity).
With no moving parts, a piezoelectric sensor offers long-term reliability and stability. Typical frequency responses range from about 1Hz to 10kHz or more. As for the operating temperature range, even a general purpose sensor will cover -25 to 90oC.
Taking Measure
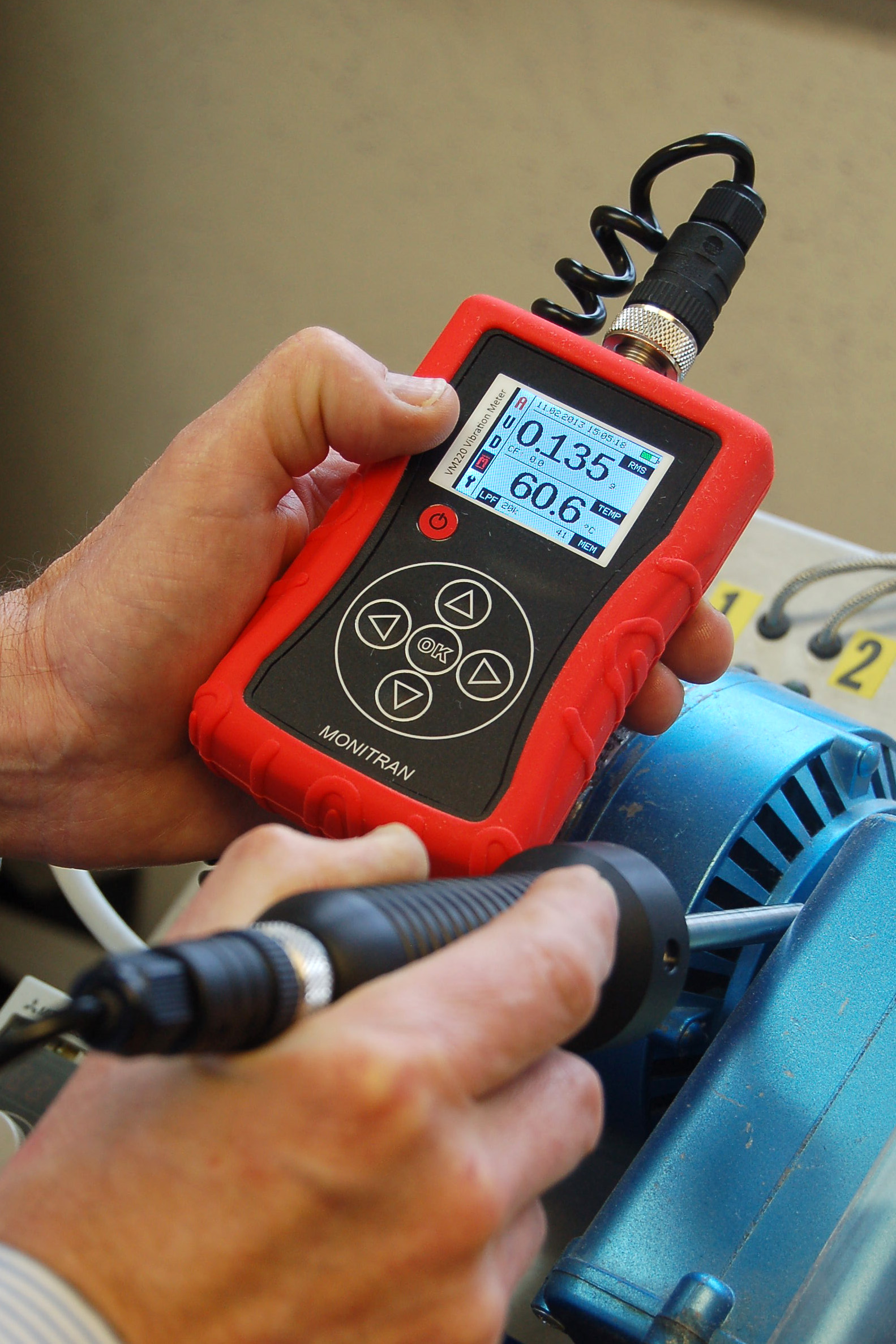
For any monitoring application it is important to make optimum use of the vibration sensor’s output range, without sacrificing sensitivity. For those interested in the maths, it is worth noting that many sensors are guaranteed to operate across the range ±80g, though they can typically experience far greater forces without fear of damage.
Assuming a sensor’s sensitivity is 100mV/g the output will swing between -8 and 8V across its declared operating range. However, if the sensor is likely to be exposed to no more than ±8g then it would be wiser to select a sensor with a sensitivity of 1V/g as the output voltage swing will provide better resolution (10x in fact) of the vibration levels.
Accordingly, if you are considering mounting vibration sensors onto a pump or motor as part of your CBPM strategy it is always worth measuring the vibration levels first. For this purpose a hand-held instrument like the just-launched MTN/VM220 will certainly fit the bill.
Conforming to ISO10816-3, the MTN/VM220 can measure and store readings for vibration (as acceleration, velocity or displacement) and temperature against a real-time clock. It is supplied with a probe into which is integrated a dual-output, general purpose sensor, the MTN/2200T (with default sensitivities of 100mV/g and 10mV/oC) and to which can be attached a magnetic base or spike.
Such a hand-held instrument is therefore very useful for establishing the normal operating conditions of machinery before installing vibrations sensors on a permanent basis or for maintenance engineers taking readings on a scheduled basis, as part of their CBPM processes.