Andy Anthony, Managing Director of Monitran, discusses how intrinsically safe sensors and a condition monitoring system are safeguarding plant and equipment.
Monitoring the condition of machinery is a practical means of protecting plant and equipment against unexpected failure, as changes in vibration levels or temperature often provide the earliest indication that maintenance is necessary. However, and as most readers will be aware, when the machinery is in a hazardous environment, such as an ATEX zone II, intrinsically safe sensors must be used.
For instance, a new biomass power station is soon to come online in the north of England. Fuel will be transported to the station’s burners via a rail load-out system which, in addition to rail carts, also includes hoppers, conveyors and feeders.
Keen to protect the rail load-out system, the operator turned to sensors OEM Monitran and engineering reliability specialists Drive Management Services (DMS) to develop a conditioning monitoring system to interface with the site’s Supervisory Control and Data Acquisition (SCADA) system. It was determined that multiple assets should be monitored for rises in vibration and temperature levels. The assets include motors, gearboxes, fan assemblies and bearing housings. To measure the levels it was decided to use 39 MTN/2285IT-4P dual output sensors (see figure 1) as permanent fixtures on the assets. Each sensor was sized such that its output is about 80% of maximum when the asset on which it is mounted is operating under normal conditions.
The majority of the sensors wire into local junction boxes, which in turn connect to a wall-mounted microprocessor-based condition monitoring unit, located in the site’s Motor Control Centre (MCC). The condition monitoring unit was built and pre-calibrated by Monitran in High Wycombe and whilst the MCC is not an ATEX II zone consideration was given to the fact that the unit is electrically connected to sensors which are in a hazardous environment; therefore Zener barriers have been employed to supress any voltages that could potentially cause a spark.
The unit connects, via Modbus TCP Ethernet, to the site’s SCADA, in which realistic alarm levels were set; not too high, so that developing faults would go undetected for too long, and not too close to normal operating levels that false alarms might occur. The SCADA also has a ‘look-back’ history that can also be accessed to determine at what rate any of the conditions being monitored might be changing.
Although the overall condition monitoring system was a custom build, developed specifically for the biomass rail load-out application, the condition monitoring unit used incorporates much of the technology at the heart of Monitran’s recently launched MTN/5000.
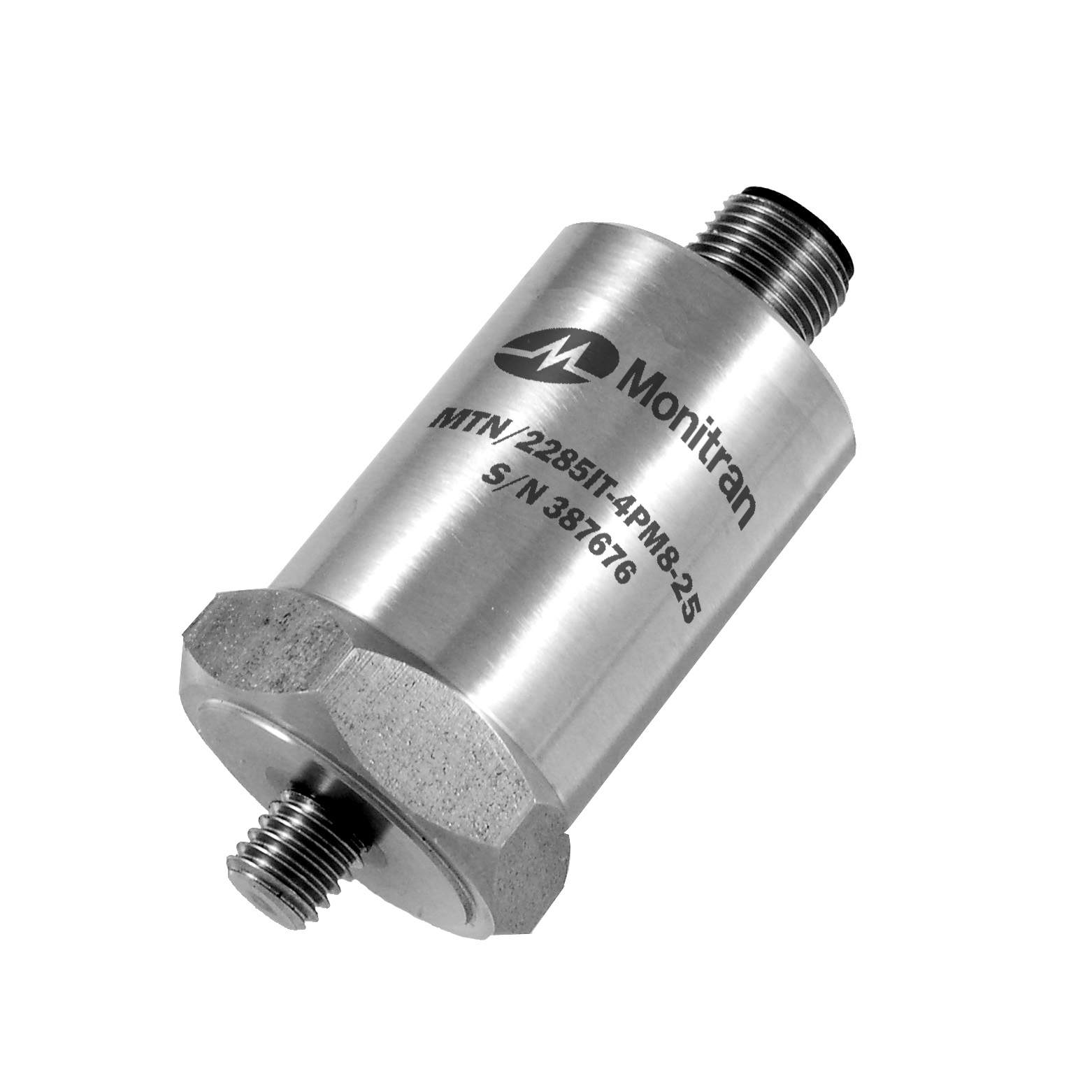
Figure 1. Certified to ATEX and IECEx Group II, the MTN/2285IT-4P is an intrinsically safe dual output sensor with a 4-20mA DC current output proportional to velocity (mm/s) or acceleration (mm/s/s) and a DC voltage proportional to temperature.
Mine of Information
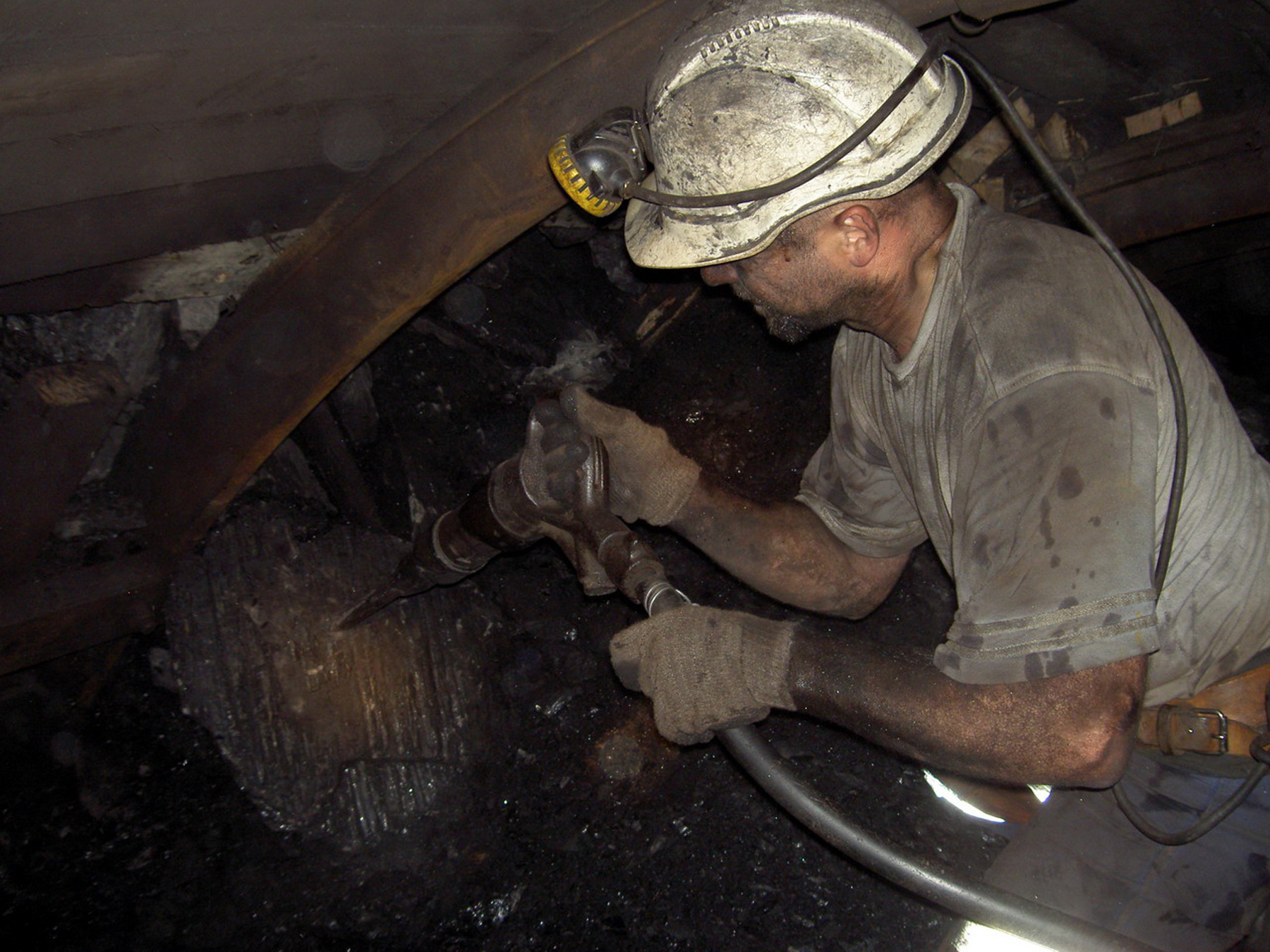
Monitoring temperature and vibration levels, using intrinsically safe sensors, can also help protect plant and equipment in the coal mining industry; where extensive conveyor belt systems are used to transport coal from the workface to the shafts. Also, analysis of the vibration signatures can provide an understating of the nature of any developing fault, such as such as a failing motor, gearbox or bearing.