A newly developed condition monitoring system is proving its worth in the dairy industry.
Adopting a condition-based predictive maintenance (CBPM) strategy is widely recognised as the best way of protecting expensive plant and equipment - particular that which is required to operate 24/7 - against unexpected failure and as a means of better scheduling servicing.
Of all conditions that might be monitored, vibration levels, or rather changes therein, tend to provide the earliest indication of wear and tear, and monitoring systems are available that can raise alarms so that engineers can investigate the causes.
Stork Food & Dairy Systems is a keen advocate of CBPM. The company specialises in the development and support of integrated processing and filling lines for the dairy and other industries. The company has 40 Dairyfill rotary fillers in use with UK-based customers. These typically operate non-stop and if they do need to shut-down outside of scheduled maintenance it creates considerable and costly logistical problems.
Luke Axel-Berg, Director - Sales UK and Northern Europe for Stork, comments: “A filler is a complex machine, with several gearboxes and bearings, and most are operating at speeds of up to 300 2-litre bottles per minute.”
For several years Stork has appreciated the value of monitoring vibration levels to determine the health of its fillers. However, in 2009, the company took CBPM to a new level. Working with the Institute of Industrial Research (IIR, now known as the Centre for Intelligent Data Solutions), which operates out of the University of Portsmouth, Stork began developing an advanced condition monitoring system called ‘Virtual Engineer’ and for which it received funding under the UK Government’s Knowledge Transfer Partnership (KTP).
An early challenge was to determine how many vibration sensors should be used and where best to position them. Here, Stork turned to Monitran, the UK-based OEM of sensors. Monitran made a site visit to see a Dairyfill machine in operation and, based on its observations and experience, recommended the use of 16 mechanically mounted sensors per machine. These are all stainless steel, single axis, low-profile, industrial sensors with integral cables and sealed to IP65.
What, where and why
The sensor mounting locations include the main bearing and hub, main drive motor, drivetrain (including block bearings and gearboxes), capper top and bottom bearing.
For data collection purposes it was decided to initially monitor three fillers. Axel-Berg continues: “Our team fitted the sensors to the selected filling machines and used HBM data acquisition units, which can cater for up to 16 analogue inputs, to convert the sensors’ analogue outputs to 24-bit resolution digital.”
The vibration levels are sampled at a nominal 3kHz and data is then streamed over the internet to a data centre at the University of Portsmouth. By sampling at such a high frequency it was possible to build quickly a detailed picture of ‘normal’ behaviour, on a machine-by-machine basis, for different modes of operation.
During the first year, anomaly detection algorithms looking for signs of deviation from normal behaviour identified six conditions which, if left unchecked, would have led to catastrophic failures. These conditions included two instances of developing main bearing failures, water in a gearbox and a universal joint out of balance.
Moreover, a developing gearbox fault was detected on a machine that was also being protected by a third party complex spectrum analysis warning system. It was unaware of the worsening condition as the gear in question rotates at about 7rpm; a frequency sufficiently low to be masked by the ‘noise threshold’.
Since the initial trial period, a further eight conditions have been detected. Axel-Berg notes: “These were typically more of the same. However, on one machine, we encountered some previously unseen spurious vibrations. Upon investigation the source was found to be a fault developing in a height adjustment system, which we’d not set out to monitor.”
Axel-Berg goes on to say this was a real bonus. It reinforced Stork’s conviction that as time goes on, and a clear picture of normal behaviour and known faults is established, any new developing vibration patterns must be the tell-tale signs of a new fault. “And good predictive maintenance is all about not being taken by surprise.”
As well as helping avoid unscheduled repairs, the intelligence gathered from the three machines aided greatly in not only their maintenance but also the other 37 fillers.
And there’s more…
Most recently, Monitran sensors have been fitted to a further eight fillers and Stork will be using Virtual Engineer to monitor their health.
Axel-Berg continues: “Customers old and new are starting to take the system seriously, and they’re beginning to appreciate the value it brings to their businesses.”
As for what that value is, based on the 14 failures that have been avoided, Stork estimates the savings are in excess of £2million. Axel-Berg concludes: “Virtual Engineer marks the first use of a remote, real-time, asset monitoring system within a CBPM strategy built primarily around vibration levels and signatures in a dairy application, and possibly within the food and drink industry as a whole.”
www.sfds.eu
www.monitran.com
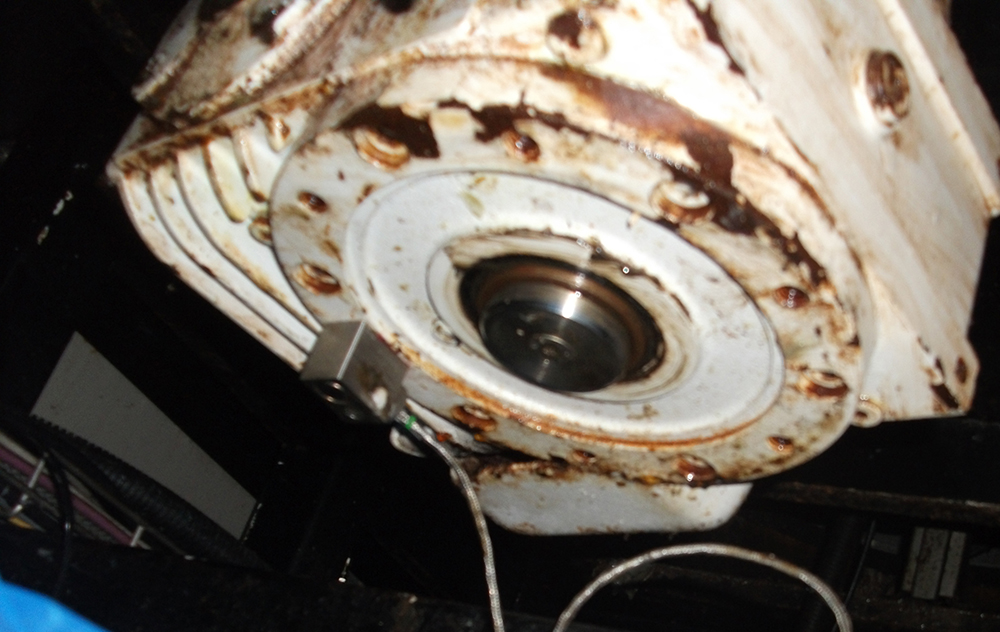
Above, one of the 16 vibration sensors used to collect data.
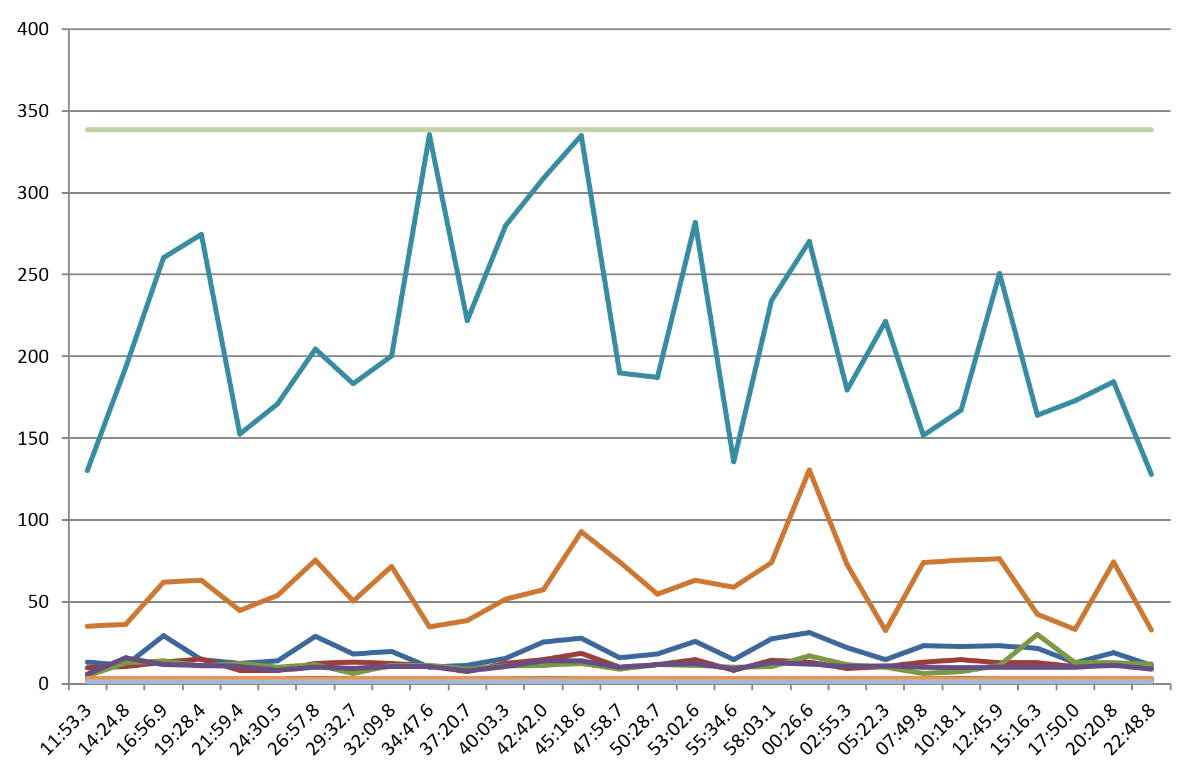
Above, data collected from one of the Dairyfill machines being monitored. The light blue trace corresponds to vibration levels on the main gear box. Investigations revealed the gearbox was oscillating on its mount.